Prüfungen im Heiztechnik-Betrieb
Facility Management: Heiztechnik » Betrieb » Prüfungen
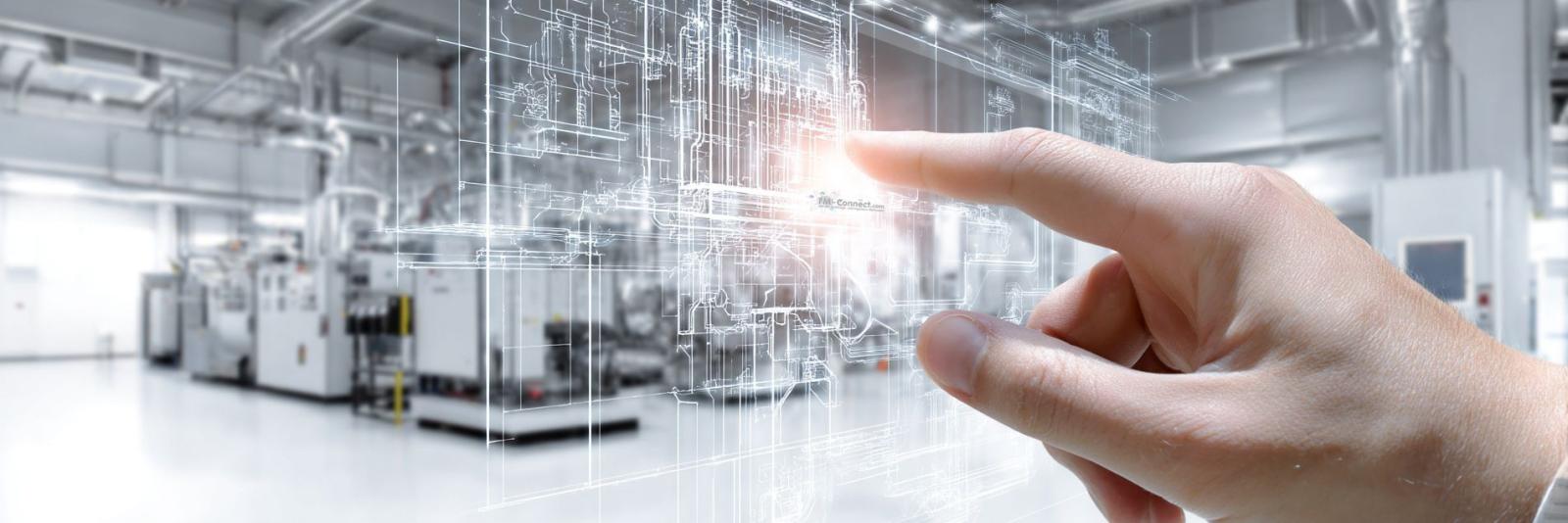
Prüfungen im Heiztechnik-Betrieb: Inspektionsregime
Die Wärmeversorgung von Produktionsanlagen, Bürogebäuden und technischen Einrichtungen muss nicht nur effizient, sondern vor allem sicher und rechtskonform betrieben werden. Prüfungen im Heiztechnik-Betrieb bezeichnen die systematischen Inspektions- und Überwachungsroutinen für Heizungsanlagen, die darauf abzielen, Betriebssicherheit, Energieeffizienz und Umweltverträglichkeit dauerhaft sicherzustellen. Zum einen sind Betreiber heiztechnischer Anlagen gesetzlich verpflichtet, regelmäßige Prüfungen durchzuführen, um Gefährdungen auszuschließen und rechtliche Auflagen zu erfüllen; zum anderen tragen optimierte Prüfregime wesentlich zur Lebenszyklusoptimierung technischer Anlagen und zur strategischen Positionierung von Unternehmen im Sinne nachhaltigen, risikoarmen Wirtschaftens bei. Auf der technischen Ebene ist deutlich, dass ein breites Spektrum an Inspektionsmaßnahmen erforderlich ist, um Heizungsanlagen sicher, effizient und zuverlässig zu betreiben – von sicherheitstechnischen Prüfungen (Druck, Leckage, Abgaswege) über Effizienz- und Emissionsmessungen bis hin zu umfassenden Anlageninspektionen und vorbeugenden Zustandskontrollen. Diese Maßnahmen greifen ineinander und ergeben ein geschlossenes Inspektionsregime, das die Anlage während ihres gesamten Lebenszyklus begleitet. Auf der rechtlichen Ebene stellen die vielfältigen deutschen Gesetze, Verordnungen und technischen Normen hohe Anforderungen an Betreiber. Die BetrSichV mit ihren Prüfpflichten für Druckanlagen, die BImSchV mit Emissionsgrenzwerten und Messvorgaben, das GEG mit energetischen Inspektionspflichten, die TRGI mit ihren Sicherheitsstandards für Gas sowie VDI- und DIN-Regelwerke bilden gemeinsam ein engmaschiges Netz an Vorgaben, dem nur mit systematischem Compliance-Management zu entsprechen ist. Die Nichteinhaltung kann gravierende rechtliche Folgen nach sich ziehen – umgekehrt schafft die penible Erfüllung der Prüfpflichten Rechtssicherheit und reduziert Haftungsrisiken signifikant.
Die Maxime muss lauten, Prüfungen nicht als lästige Pflicht abzutun, sondern als integralen Bestandteil einer Kultur exzellenter Betriebsführung zu begreifen. Sie leisten einen entscheidenden Beitrag dazu, dass Heiztechnik sicher, nachhaltig und effizient betrieben werden kann – heute und in Zukunft.
Prüfprozesse im Heiztechnikbetrieb
Rechtliche und normative Grundlagen der Prüfpflichten
Ein Verständnis der Prüfungen im Heiztechnik-Betrieb erfordert zunächst einen Blick auf die rechtlichen Rahmenbedingungen und anerkannten Normen, welche die Betreiberpflichten in Deutschland prägen. Betreiber von Heizungsanlagen sind verpflichtet, eine Vielzahl von Gesetzen, Verordnungen und technischen Regeln einzuhalten. Im Folgenden werden die wichtigsten Vorschriften und Normen umrissen:
Betriebssicherheitsverordnung (BetrSichV): Die BetrSichV bildet das Kernstück der sicherheitstechnischen Anforderungen beim Betrieb technischer Anlagen. Sie gilt sowohl für Arbeitsmittel als auch für überwachungsbedürftige Anlagen (letztere umfassen u. a. Druckanlagen wie Dampfkessel und Druckbehälter). Gemäß BetrSichV darf eine überwachungsbedürftige Anlage (z. B. ein Heizkessel, der als Druckgerät einzustufen ist) erst betrieben werden, nachdem der Arbeitgeber eine Gefährdungsbeurteilung durchgeführt, alle erforderlichen Schutzmaßnahmen ergriffen und die Sicherheit der Anlage nach dem Stand der Technik festgestellt hat. Weiterhin fordert die BetrSichV, dass für solche Anlagen vor der Inbetriebnahme sowie wiederkehrend Prüfungen durchgeführt werden. Die Prüfungen müssen durch eine zugelassene Überwachungsstelle (ZÜS) oder – je nach Anlagentyp – durch eine entsprechend befähigte Person erfolgen. Die Verordnung regelt in Anhang 2 detailliert die Arten und Intervalle dieser Prüfungen. So sind beispielsweise bei Druckbehälteranlagen eine äußere Sichtprüfung, eine innere Prüfung sowie eine Festigkeitsprüfung (Druckprüfung) in bestimmten Fristen durchzuführen. Typischerweise schreibt die BetrSichV vor, dass eine innere Prüfung mindestens alle 5 Jahre und eine Druckprüfung alle 10 Jahre stattfinden muss. Für Dampfkesselanlagen und größere Heizkessel können strengere oder zusätzliche Prüfintervalle gelten. Die konsequente Umsetzung der BetrSichV-Prüfpflichten ist zentral, um Unfälle (etwa durch Überdruck oder Materialversagen) zu vermeiden und haftungsrechtliche Konsequenzen auszuschließen.
Technische Regeln für Betriebssicherheit (TRBS): Als Ausführungshilfen zur BetrSichV präzisieren TRBS die Anforderungen an Prüfungen. Beispielsweise definiert TRBS 1201 Verfahren für wiederkehrende Prüfungen druckbeaufschlagter Anlagen und erlaubt unter bestimmten Voraussetzungen risikobasierte Anpassungen der Prüffristen im Rahmen der Gefährdungsbeurteilung. Betreiber können – gestützt auf TRBS und sachverständige Beratung – Prüffristen verlängern oder verkürzen, sofern die Sicherheit gewährleistet bleibt. Diese Flexibilisierung unterliegt jedoch engen Grenzen der technischen Regelkonformität und behördlicher Genehmigung.
Verordnung über Immissionsschutz (1. BImSchV): Die Erste Verordnung zur Durchführung des Bundes-Immissionsschutzgesetzes, bekannt als Kleinfeuerungsanlagen-Verordnung (1. BImSchV), regelt die zulässigen Emissionen und energetischen Kennwerte von Heizungsanlagen bis in den mittleren Leistungsbereich. Betreiber solcher Feuerungsanlagen (Öl, Gas, feste Brennstoffe) unterliegen regelmäßigen Emissions- und Effizienzprüfungen, die typischerweise vom bevollmächtigten Bezirksschornsteinfeger oder einer autorisierten Fachkraft vorgenommen werden. Seit der Novelle von 2010 gelten erweiterte Prüfintervalle und verschärfte Grenzwerte: Gas- und Ölheizungen müssen auf Abgasverlust und Schadstoffausstoß geprüft werden – bei neuen Anlagen alle drei Jahre, bei älteren (über 12 Jahre alt) alle zwei Jahre. Zugleich wurden maximale Abgasverlust-Grenzwerte festgelegt, etwa 11 % bei kleinen Heizkesseln (4–25 kW) und 9 % bei größeren Anlagen >50 kW. Moderne Brennwertkessel mit sehr hohem Wirkungsgrad sind aufgrund ihrer geringen Verluste teilweise von der Abgasverlustmessung befreit, jedoch müssen auch sie regelmäßig hinsichtlich Sicherheit überprüft werden. Hier greift ergänzend die Kehr- und Überprüfungsordnung (KÜO): Nach KÜO ist z. B. bei raumluftabhängigen Feuerungsanlagen (Kessel, die Verbrennungsluft aus dem Aufstellraum entnehmen) jährlich eine sicherheitstechnische Überprüfung der Abgaswege durchzuführen; bei raumluftunabhängigen Brennwertgeräten genügt ein Turnus von zwei Jahren, und Anlagen mit selbstüberwachender Regelung können alle drei Jahre überprüft werden. Diese Sicherheitsprüfungen durch den Schornsteinfeger gewährleisten, dass Abgassysteme frei von Verschlüssen sind und die CO-Emission unterhalb kritischer Schwellen bleibt – essentiell für den Schutz der Nutzer und der Umgebung.
Gebäudeenergiegesetz (GEG) und ehemalige Energieeinsparverordnung (EnEV): Das GEG (in Kraft seit November 2020) vereint und aktualisiert die vorherigen Regelungen der EnEV, des EnEG und des EEWärmeG. Es adressiert die energetische Performance von Gebäuden und stellt Anforderungen an die Anlagentechnik. Für den Heiztechnik-Betrieb relevant sind insbesondere Vorschriften zur Effizienzüberwachung und Modernisierungspflicht. So schreibt das GEG vor, dass Betreiber alter Heizkessel (in der Regel älter als 30 Jahre, ausgenommen Niedertemperatur- und Brennwertkessel) diese austauschen müssen, da sie die heutigen Effizienzanforderungen nicht mehr erfüllen (§72 GEG, vormals §10 EnEV). Darüber hinaus wurde im Zuge der Energiesicherungsmaßnahmen 2022/23 eine Pflicht zur Heizungsüberprüfung (Heizungs-Check) eingeführt: Nach § 12 der EnSimiMaV (Verordnung zur Sicherung der Energieversorgung) mussten Eigentümer von Gasheizungen bis Herbst 2024 eine energetische Inspektion ihrer Anlage nach dem Standard der DIN EN 15378 durchführen lassen. Diese Pflicht wurde ab Oktober 2024 in § 60b GEG überführt. Der Heizungscheck gemäß DIN EN 15378 ist ein standardisiertes Verfahren zur umfassenden Bewertung der Energieeffizienz eines Wärmeerzeugers und des Heizsystems – von der Kesselauslegung bis zu Regelung und Verteilung. Bereits seit EnEV 2007 galt die Anforderung, dass zentralen Heizungsanlagen >20 kW Nennleistung, die älter als 15 Jahre sind, eine einmalige energetische Inspektion der gesamten Anlage durchlaufen müssen. Diese Inspektion, oft vom Schornsteinfeger oder Energieberater durchgeführt, identifiziert Effizienzschwachstellen (z. B. überdimensionierte Kessel, fehlende Regelungen, hydraulisches Ungleichgewicht) und gibt dem Betreiber Modernisierungsempfehlungen. Die Einhaltung dieser Vorgaben wird stichprobenartig von Behörden überprüft und bei Nichteinhaltung drohen ordnungsrechtliche Konsequenzen. Damit ergänzt das GEG die betriebssicherheitsrechtlichen Prüfpflichten um den Aspekt der Energieeffizienz und Klimaschutz-Compliance.
DVGW-TRGI (Technische Regel für Gasinstallationen): Heiztechnik in Industrie und Gewerbe basiert häufig auf Gasfeuerungsanlagen, weshalb die Sicherheit der Gasversorgung ein kritischer Punkt ist. Die vom Deutschen Verein des Gas- und Wasserfaches (DVGW) herausgegebene TRGI (Arbeitsblatt G 600) legt anerkannte Regeln für Planung, Bau und Betrieb von Gasleitungsanlagen fest. Besonders relevant sind die Vorgaben zur Dichtheitsprüfung von Gasleitungen. Gemäß TRGI 2018 müssen im Betrieb befindliche Gas-Innenleitungen mindestens alle 12 Jahre einer Gebrauchsfähigkeitsprüfung (Leckratenmessung) unterzogen werden. Diese Prüfung (bis 100 hPa Betriebsdruck) stellt sicher, dass keine unentdeckten Leckagen vorliegen, die Explosionsgefahr oder Verluste verursachen würden. Ergänzend empfiehlt die TRGI eine jährliche Sichtkontrolle (sogenannte Hausschau) durch den Betreiber oder Fachmann, um offensichtliche Mängel (Korrosion, mechanische Beschädigungen, Gasgeruch etc.) frühzeitig zu erkennen. Die TRGI-Vorgaben sind zwar privatrechtliche technische Regeln, jedoch haben sie faktisch Normcharakter: Sie konkretisieren die Verkehrssicherungspflichten des Betreibers und werden im Schadenfall oder gegenüber Aufsichtsbehörden als Maßstab für den „anerkannten Stand der Technik“ herangezogen. Die Verpflichtung zur 12-Jahres-Prüfung wurde erst in den letzten Revisionen der TRGI ausdrücklich als Pflicht hervorgehoben, was zeigt, dass in der Praxis zuvor teils Nachholbedarf bei der Kontrolle von Bestands-Gasleitungen bestand. Heute kann durch den Einsatz moderner, automatisierter Druckmessgeräte die Gasleitungsprüfung zügig und präzise erfolgen, was Betreibern die Erfüllung dieser Normauflage erleichtert.
VDI-Richtlinien und DIN-Normen: Über die bindenden Gesetze hinaus müssen Betreiber von Heizungsanlagen die anerkannten Regeln der Technik beachten. Dazu zählen insbesondere Richtlinien des Verein Deutscher Ingenieure (VDI) und einschlägige DIN-/EN-Normen. Im Bereich Heiztechnik-Betrieb sind mehrere Regelwerke relevant: Die Richtlinienreihe VDI 3810 (Betreiben und Instandhalten von gebäudetechnischen Anlagen) widmet sich verschiedenen Anlagengruppen. VDI 3810 Blatt 3 (Ausgabe 2018) behandelt spezifisch hydraulisch betriebene heiztechnische Anlagen (Warmwasserheizungen) und definiert Betreiberpflichten, Sicherheitsanforderungen sowie Instandhaltungsmaßnahmen. Diese Richtlinie betont, dass der Betreiber einer Heizungsanlage alle einschlägigen Gesetze und technischen Regeln einhalten und erforderliche Prüfungen veranlassen muss (z. B. solche nach dem Schornsteinfeger-Handwerksgesetz und anderen Vorschriften). VDI 3810-3 verweist ausdrücklich auf die Inspektion nach DIN EN 15378: Gemäß Anhang A der Richtlinie werden Inspektionen einer Heizungsanlage in eine einmalige Gesamtsystem-Inspektion und wiederkehrende Inspektionen des Wärmeerzeugers unterteilt. Die einmalige Inspektion entspricht dem erwähnten Heizungscheck, während die periodischen Inspektionen des Wärmeerzeugers z. B. die regelmäßigen Effizienz- und Emissionsmessungen (durch Schornsteinfeger) und die sicherheitstechnischen Kontrollen umfassen. Daneben geben VDI-Richtlinien wie VDI 2035 (Vermeidung von Kesselstein und Korrosion), VDI 2047 (Kühltürme – aber für Heiztechnik weniger relevant) oder VDI 6023 (Hygiene in Trinkwassererwärmungsanlagen) spezifische technische Empfehlungen, die bei Heizkesseln und Warmwasserbereitern in bestimmten Kontexten einzuhalten sind. Im Rahmen dieser Arbeit ist besonders der Aspekt der Instandhaltungssystematik zu nennen: Nach DIN 31051 bzw. DIN EN 13306 gliedert sich Instandhaltung in die Grundmaßnahmen Wartung, Inspektion, Instandsetzung und Verbesserung. Inspektion ist dabei definiert als Untersuchung zur Feststellung und Beurteilung des Ist-Zustands einer Anlage (ohne Eingriff), während Wartung der Bewahrung des Soll-Zustands (durch z. B. Reinigungen, Justagen) dient. Prüfungen im Heiztechnik-Betrieb umfassen demnach vor allem Inspektionsmaßnahmen im Sinne dieser Norm – ergänzt durch daraus abgeleitete Wartungs- oder Instandsetzungsarbeiten. Auch die DIN EN 15378 selbst (Heizungssysteme in Gebäuden – Inspektion von Kesseln und Heizungsanlagen) ist zu erwähnen: Sie liefert ein normiertes Verfahren für den Heizungs-Check und definiert Kennzahlen und Checklisten, anhand derer die Anlageneffizienz bewertet wird. Zusammen mit nationalen Anhängen (ehemals DIN 4792) stellt diese Norm ein Werkzeug für Energieberater und Schornsteinfeger dar, um die Qualität und Vergleichbarkeit der Inspektionsergebnisse sicherzustellen.
Zusammenfassend lässt sich festhalten, dass die Prüfungsregime im Heiztechnik-Betrieb auf einem dichten Netz gesetzlicher Vorgaben und technischer Standards basieren. Die Betreiberverantwortung erfordert die Kenntnis und Anwendung all dieser Regeln – von der BetrSichV über BImSchV/Schornsteinfegerrecht, GEG/EnEV bis zu TRGI, VDI und DIN-Normen. Im nächsten Abschnitt wird darauf aufbauend betrachtet, welche konkreten Prüfarten und Inspektionsmaßnahmen sich daraus für den praktischen Betrieb von Heizungsanlagen ergeben.
Arten von Prüfungen und Inspektionsregimen in Heizungsanlagen
Heiztechnische Anlagen in industriellen Einrichtungen unterliegen einer Vielzahl an Prüfungen, die unterschiedlichen Zwecken dienen. Grob lassen sich folgende Kategorien unterscheiden: Sicherheitsprüfungen, Effizienz- und Emissionsmessungen, hydraulische Abgleiche sowie Integritäts- und Zustandsbewertungen. Diese Kategorien überschneiden sich teilweise, ergänzen einander jedoch im Sinne eines ganzheitlichen Inspektionskonzepts. Im Folgenden werden die wichtigsten Prüfungsarten erläutert:
Sicherheitsüberprüfungen und Schutzsystem-Prüfungen
Sicherheitsprüfungen zielen darauf ab, akute Gefahren im Betrieb von Heizungsanlagen zu vermeiden.
Hierzu zählen:
Druck- und Festigkeitsprüfungen: Bei geschlossenen Warmwasserheizungen, Dampfkesseln oder Heißwassererzeugern besteht die Gefahr von Überdruck und Berstversagen. Dementsprechend sind druckführende Komponenten regelmäßigen Prüfungen zu unterziehen. Wie bereits erläutert, verlangt die BetrSichV für überwachungsbedürftige Druckgeräte (z. B. Großwasserkessel, Druckausdehnungsgefäße) in der Regel eine innere Prüfung alle 5 Jahre und eine hydraulische Druckprobe alle 10 Jahre. Bei diesen Prüfungen wird zum Beispiel ein Heizkessel drucklos geöffnet, auf Korrosionsschäden und Materialrisse untersucht (innere Prüfung) und anschließend mit Wasser über den Betriebsdruck hinaus abgedrückt, um die Festigkeit zu verifizieren. Besonders sicherheitsrelevante Bauteile wie Sicherheitsventile müssen oft noch häufiger getestet werden – teils jährlich durch Simulationsauslösung, um sicherzustellen, dass sie im Überdruckfall ansprechen. Betriebe bestellen hierfür entweder externe Sachverständige (ZÜS) oder schulen eigene befähigte Personen, soweit zulässig. Auch Rohrleitungen für brennbare Gase (Gasverteilung im Betrieb) gehören zu den überwachungsbedürftigen Anlagen; diese Leitungen müssen nach BetrSichV vor Inbetriebnahme und nach wesentlichen Änderungen geprüft und im Betrieb regelmäßig inspiziert werden. Summa summarum dienen solche Druckprüfungen dazu, das Risiko von Explosionen oder mechanischen Katastrophen proaktiv einzudämmen.
Leckage- und Dichtheitsprüfungen: Neben dem mechanischen Druckbestand ist die Dichtheit von Brennstoffleitungen ein kritischer Sicherheitsfaktor. Wie ausgeführt, fordert die TRGI alle 12 Jahre eine professionelle Prüfung der Gebrauchsfähigkeit von Gasleitungen. Dabei wird entweder mittels definierter Druckabfallmessung oder kontinuierlicher Leckratenmessung festgestellt, ob die Gasverluste innerhalb zulässiger Grenzen liegen. In industriellen Heizzentralen mit verzweigtem Rohrleitungsnetz kann dies ein aufwendiger Prozess sein, der abschnittsweise durchgeführt wird. Moderne Messgeräte vereinfachen den Ablauf erheblich, indem sie automatisiert Druckänderungen registrieren und klassifizieren (Ergebnis: „unbeschränkt gebrauchsfähig“ bis „nicht gebrauchsfähig“). Neben der periodischen Vollprüfung sehen die Regeln auch einfachere Verfahren vor: z. B. die jährliche Hausschau durch unterwiesenes Personal, bei der oberflächliche Undichtigkeiten durch Besichtigen aller Armaturen (ggf. mit Lecksuchspray) erkannt werden können. Nicht zu vergessen sind flüssigbrennstoffbetriebene Heizungen (Heizöl): Deren Tankanlagen unterliegen dem Wasserhaushaltsgesetz und den Verordnungen der Länder (VAwS). Dort sind ebenfalls Dichtheitsprüfungen der Tanks und Sicherheitseinrichtungen (z. B. Grenzwertgeber) im Turnus von meist 5 Jahren vorgeschrieben, um Leckagen von Heizöl zu verhindern – ein Aspekt, der in industriellen Betrieben mit eigenem Tankvorrat eine Rolle spielt.
Elektrische Sicherheit und Steuerung: Heizungsanlagen umfassen elektrische Komponenten wie Brennersteuerungen, Pumpen, Ventile und Sicherheitseinrichtungen (z. B. Flammenwächter, Druckwächter). Die regelmäßige Prüfung dieser Steuer- und Regeleinrichtungen stellt sicher, dass z. B. ein Flammenausfall sofort detektiert und die Gaszufuhr gesperrt wird. Nach VDE-Vorschriften (und teils DGUV-Regeln) sollten elektrische Anlagen – dazu zählen auch die Schalttafeln von Heizkesseln – in bestimmten Abständen von einer elektrotechnisch befähigten Person geprüft werden (Isolationswiderstand, Schutzleiter, Funktion der Not-Aus Schalter etc.). Zwar fällt dies eher in den Bereich allgemeiner Arbeitssicherheit, ist aber integraler Bestandteil des sicheren Heizungsbetriebs in einem Industriebetrieb.
Schornstein- und Abgasanlagenprüfung: Die sichere Abführung der Verbrennungsabgase wird durch den Schornsteinfeger im Rahmen der KÜO-Überprüfung gewährleistet. Wie oben erwähnt, unterscheidet man je nach Gerätetyp jährliche oder zweijährliche Abgaswegeüberprüfungen. Der Kaminkehrer kontrolliert hierbei, ob Abzüge frei sind und die Verbrennung einwandfrei verläuft (z. B. durch CO-Messung im Abgas). In industriellen Heizhäusern mit hohen Kaminen können zusätzliche Prüfungen erforderlich sein, etwa statische Begutachtungen des Schornsteins oder Messungen der Kaminzugverhältnisse durch Immissionsschutzbeauftragte, besonders wenn mehrere Kessel an einem Zug hängen.
Es sind Sicherheitsprüfungen obligatorisch, um akute Gefährdungen auszuschließen. Sie unterliegen festen Intervallen und sind meist durch Gesetz geregelt. Die Nichteinhaltung dieser Prüfpflichten kann gravierende Folgen haben – von Bußgeldern und Betriebsstilllegungen bis hin zur persönlichen Haftung der verantwortlichen Personen im Schadensfall. So legt etwa § 823 BGB als allgemeine zivilrechtliche Verkehrssicherungspflicht fest, dass der Betreiber einer potenziell gefährlichen Anlage alle zumutbaren Vorkehrungen treffen muss, um Dritte vor Schaden zu bewahren. Regelmäßige sicherheitstechnische Prüfungen sind ein zentrales Element, dieser Pflicht nachzukommen.
Effizienzprüfungen und Emissionsmessungen
Ein zweiter Schwerpunkt im Prüfwesen sind Maßnahmen zur Leistungsüberwachung der Heizanlage, insbesondere im Hinblick auf energetische Effizienz und umweltrelevante Emissionen:
Abgasverlust- und Wirkungsgradmessungen: Die meisten Industrieliegenschaften nutzen Heizkessel im Leistungsbereich von einigen 100 kW bis hin zu mehreren MW (z. B. in Form von Kaskaden oder KWK-Anlagen). Durch Abgasmessungen wird festgestellt, wie effizient die Verbrennung abläuft. Ein hoher Abgasverlust (Anteil der Wärme, der ungenutzt durch den Schornstein entweicht) deutet auf einen schlechten Kesselwirkungsgrad hin. Nach 1. BImSchV darf der Abgasverlust bestimmte Grenzwerte nicht überschreiten (9–11 %, je nach Kesselgröße). Die Messung erfolgt durch den Schornsteinfeger oder Messdienst: Mit einem geeichten Abgasanalysegerät werden Abgastemperatur, O₂/CO₂-Gehalt und CO-Konzentration gemessen und der Verlust berechnet. Moderne Brennwertanlagen liegen oft unterhalb des Messbereichs für Abgasverlust, so dass die Verordnung sie ausnimmt – hier beschränkt sich die Prüfung dann auf die Einhaltung der CO-Grenzwerte und eine Funktionskontrolle. In der Industrie, wo ggf. älteres Kessel-Equipment eingesetzt wird, sind die Abgasmessungen ein wichtiges Diagnoseinstrument: Ein sich verschlechternder Abgaswert kann z. B. auf Verschmutzungen im Wärmetauscher, Fehleinstellungen oder Brennerverschleiß hindeuten. Somit dienen diese Prüfungen nicht nur der amtlichen Kontrolle, sondern auch der Instandhaltungsplanung (Stichwort: vorausschauende Wartung).
Schadstoff-Emissionsmessungen: Neben CO (Kohlenmonoxid) als Indikator für unvollständige Verbrennung müssen ggf. auch Stickoxide (NOₓ) und bei Öl- oder Festbrennstoffen Rußpartikel überwacht werden. Die 1. BImSchV enthält Grenzwerte für NOₓ-Emissionen in Abhängigkeit von Brennstoff und Leistungsklasse. In kleineren Anlagen übernimmt dies ebenfalls der Schornsteinfeger im Rahmen der wiederkehrenden Messung. In größeren Feuerungsanlagen (etwa über 1 MW Feuerungswärmeleistung) greift die 13. BImSchV bzw. für mittelgroße Anlagen die 44. BImSchV, die anspruchsvollere kontinuierliche Messungen durch Messstellen vorschreiben können. Für ein Facility Management im industriellen Kontext bedeutet das: Es müssen Verträge mit entsprechend zugelassenen Umweltmessstellen bestehen, die jährlich (oder kontinuierlich via Messfühler) die Emissionen protokollieren. Das Emissionsmonitoring ist somit Bestandteil des Prüfregimes – es stellt sicher, dass der Betrieb umweltgesetzlichen Auflagen genügt und trägt zum Nachhaltigkeitsmanagement des Unternehmens bei.
Energieverbrauchs- und Effizienzkontrollen: Jenseits der behördlich geforderten Abgasmessungen führen fortschrittliche Betreiber eigene Effizienzprüfungen durch. Dazu gehört etwa der jährliche Wirkungsgradtest unter Volllast und Teillast, um zu prüfen, ob der Kessel noch in seinem Auslegungsoptimum arbeitet. Oft geschieht dies im Zuge der Wartung durch Fachfirmen, die z. B. den Feuerungswirkungsgrad ermitteln und mit früheren Werten vergleichen. Ebenso kann ein Heizungs-Check nach DIN EN 15378 durchgeführt werden (sofern nicht ohnehin gesetzlich vorgeschrieben), der über die Messwerte hinaus qualitative Kriterien bewertet – z. B. die Regelungseinstellungen, die Dämmung der Verteilleitungen oder die hydraulische Einbindung von Pumpen. Solche Effizienz-Prüfungen ermöglichen es, Energiesparpotenziale zu identifizieren. Beispielsweise könnte festgestellt werden, dass ein Kessel überdimensioniert ist und ständig taktet; der Inspektionsbericht würde dann empfehlen, einen kleineren oder modulierenden Brenner einzusetzen. Gerade vor dem Hintergrund steigender Energiepreise ist diese Form der Inspektion heute strategisch wichtig. Viele Unternehmen haben im Rahmen von Energiemanagementsystemen (ISO 50001) regelmäßige Überprüfungen der Hauptverbraucher – zu denen Heizkessel oft zählen – institutionalisiert.
Hydraulischer Abgleich als Prüfmaßnahme: Der hydraulische Abgleich von Heizungsanlagen – eigentlich eine Optimierungsdienstleistung – kann hier ebenfalls genannt werden, da er in manchen Fällen als verpflichtende Maßnahme auftritt. So fordern etwa Förderprogramme (BEG der KfW/BAFA) und teils auch gesetzliche Vorgaben, dass nach einer Kesselmodernisierung ein hydraulischer Abgleich durchgeführt und nachgewiesen wird. Ein hydraulischer Abgleich stellt sicher, dass alle Wärmeverbraucher im System mit der richtigen Durchflussmenge versorgt werden, was Überhitzungen und Rücklaufverluste vermeidet. Obwohl dies kein „Prüfen“ im engeren Sinne ist, beinhaltet er doch ein Messen (der Durchflüsse, Druckverluste, Heizflächentemperaturen) und Einstellen der Anlage. Im Kontext der Inspektionsroutinen könnte man den hydraulischen Abgleich als einmalige Prüfung der Anlagenhydraulik auffassen, insbesondere nach Inbetriebnahme oder größeren Änderungen. Er trägt erheblich zur Effizienz bei und wird in der Praxis oft im Inspektionsbericht (Heizungscheck) empfohlen, falls nicht vorhanden. Für den Facility Manager bedeutet das: Einerseits Compliance mit Normen (GEG verlangt z. B., dass bei gewissen Sanierungen der Abgleich vorzunehmen ist), andererseits langfristige Einsparungen und gleichmäßigerer Betrieb.
Es dienen Effizienz- und Emissionsprüfungen der kontinuierlichen Überwachung der Anlagengesundheit aus energetischer und umwelttechnischer Sicht. Sie stellen einen fließenden Übergang von reiner Pflichterfüllung hin zur Prozessoptimierung dar. Gerade in industriellen Settings, wo Heizenergie ein Kostenfaktor und Emissionen möglicherweise genehmigungsrelevant sind, sind diese Prüfungen unerlässlich. Neben der Einhaltung gesetzlicher Grenzwerte verfolgt man damit auch das Ziel, Störungen frühzeitig zu erkennen (z. B. Brennerprobleme durch CO-Anstieg) und Wirkungsgradverluste rückgängig zu machen (z. B. Reinigung bei schlechtem Abgaswert). In einem späteren Abschnitt wird noch erörtert, wie solche Inspektionen in ein umfassendes Energiemanagement und in Lifecycle-Betrachtungen eingebettet werden können.
Prüfungen der Systemintegrität und Zustandsbewertung
Über Sicherheit und Effizienz hinaus müssen Heizungsanlagen als Ganzes in einem zuverlässigen Betriebszustand gehalten werden. Hier kommen Inspektionsmaßnahmen ins Spiel, die man als präventive Anlagenzustands-Bewertungen bezeichnen kann:
Visuelle Anlageninspektionen: In regelmäßigen Abständen – häufig jährlich oder halbjährlich – inspiziert der zuständige Haustechniker oder ein externer Servicepartner die gesamte Heizungsanlage visuell. Dabei werden etwa folgende Punkte geprüft: Zustand von Kessel und Rohrleitungen (Korrosion, Undichtigkeiten, Isolationsschäden), Zustand der Heizraumumgebung (Belüftungsöffnungen frei? Brennstofflager sicher?), Funktion der Instrumente (Manometer, Thermometer, Füllstandsanzeigen) und allgemeine Ordnung und Sauberkeit im Heizraum. Diese Durchsichten stellen sicher, dass offenkundige Mängel nicht unentdeckt bleiben. Oft werden sie anhand von Checklisten durchgeführt, die auf VDI 3810 und herstellerbezogenen Wartungsplänen basieren. Entdeckte Mängel fließen in Arbeitsaufträge für Instandsetzung ein. Solche Inspektionen sind zwar nicht immer explizit gesetzlich gefordert, erfüllen aber implizit die Betreiberpflicht zur Gefahrenabwehr und stehen in Einklang mit den VDI-Empfehlungen für bestimmungsgemäßen Anlagenbetrieb.
Thermografische Untersuchungen: Eine zunehmend genutzte Methode zur Zustandsbeurteilung ist die Infrarot-Thermografie. Bei Heizkesseln und -verteilungen kann eine Thermografie etwa Hotspots an Kesselaußenflächen (Hinweis auf Dämmdefekt oder Ablagerungen innen), ungleich beheizte Bereiche oder Wärmebrücken in der Gebäudehülle des Heizraums sichtbar machen. In industriellen Fernwärme- oder Dampfnetzen werden Thermografien eingesetzt, um Wärmeverluste und Feuchtestellen (mögliche Leckagen) entlang der Trassen zu detektieren. Diese Untersuchungen sind üblicherweise nicht vorgeschrieben, gehören aber zu einem modernen Inspektionsregime dazu, wenn es um vorausschauende Instandhaltung geht.
Schwingungs- und Geräuschmessungen: In großen Heizanlagen, besonders wenn sie in Form von BHKW (Blockheizkraftwerken) oder mit großen Gebläsebrennern ausgestattet sind, geben Schwingungs- und Geräuschpegel wichtige Hinweise auf den Zustand. Eine routinemäßige Messung von Vibrationen an Pumpen, Ventilatoren oder dem Kesselgerüst kann Verschleiß (z. B. Lagerschäden) früh anzeigen. Solche zustandsorientierten Prüfungen werden oft im Rahmen von Condition Monitoring in der Industrie angesiedelt. Zwar sind sie für rein thermische Kesselanlagen seltener, doch Pumpen (z. B. Hauptumwälzpumpen) werden in kritischen Umgebungen durchaus mit Schwingungsaufnehmern überwacht.
Wasserqualitätsprüfungen: Ein integraler Bestandteil der Systemintegrität ist die Qualität des Heizungswassers. Nach VDI 2035 und den technischen Regeln der Wasserbeschaffenheit sollte das Füll- und Umlaufwasser bestimmte Härte- und pH-Werte einhalten, um Kesselsteinbildung und Korrosion zu vermeiden. Deshalb kann man auch die regelmäßige Analyse des Kesselwassers als Prüfaufgabe verstehen. In größeren Anlagen (z. B. mit Hochtemperatur-Heißwasser) ist oft ein Wasseraufbereitungssystem vorhanden, dessen Funktion durch Wasserproben (leitfähigkeits-, Sauerstoffgehalt, Hemmstoffkonzentrationen) überprüft wird. Ein unzureichend gewarteter Wasserchemiezustand kann zu gravierenden Schäden führen; die Prüfung ist daher präventiv unabdingbar.
Dokumentationsprüfung (Anlagenbuch): Interessanterweise fordern Richtlinien wie VDI 3810 auch die Führung eines Anlagenbuchs, in dem alle relevanten Daten, Prüfungen und Ereignisse dokumentiert sind. Die regelmäßige Durchsicht der Anlagendokumentation selbst kann als eine Art „Prüfung“ betrachtet werden: Der Betreiber sollte etwa jährlich verifizieren, ob alle vorgeschriebenen Prüftermine eingehalten und im Anlagenbuch vermerkt wurden, ob Wartungsnachweise vorliegen und ob Prüfgutachten (z. B. von TÜV-Prüfungen) vollständig archiviert sind. Diese Meta-Prüfung der Dokumentation dient der eigenen Absicherung im Compliance-Sinne und stellt sicher, dass beim Eintreffen externer Auditoren oder Aufsichtsbehörden lückenlose Nachweise bereitstehen.
In Summe ergänzen solche integritätsorientierten Inspektionen die formal geforderten Prüfungen. Sie folgen dem guten Ingenieursgrundsatz, dass vorbeugen besser ist als reparieren. Durch fortlaufende Zustandsbeobachtung kann die Zuverlässigkeit der Anlage maximiert werden, Ausfälle werden unwahrscheinlicher und Restrisiken minimiert. Industrielle Facility-Manager integrieren diese Maßnahmen oft in Instandhaltungspläne, sodass z. B. neben den gesetzlich fixen Terminen (Schornsteinfeger, TÜV) auch interne vierteljährliche Rundgänge und jährliche Sonderuntersuchungen fest eingeplant sind.
Operative, rechtliche und strategische Implikationen der Prüfplichten
Die Durchführung von Prüfungen im Heiztechnik-Betrieb ist nicht nur eine technische Aufgabe, sondern hat vielfältige Auswirkungen auf den operativen Betrieb, die Rechtskonformität und die strategische Ausrichtung eines Unternehmens. In diesem Abschnitt wird analysiert, welche Implikationen sich in diesen Dimensionen ergeben und wie Facility Management damit umgeht.
Operative Aspekte im Anlagenbetrieb
Betriebsorganisation und Ressourcenplanung: Jede Prüfung – sei es eine behördlich geforderte oder eine freiwillige – erfordert operative Vorbereitung. So müssen Anlagen für bestimmte Prüfungen außer Betrieb genommen oder im Teillastbetrieb gefahren werden (z. B. Kesselabstellung für innere Inspektion). Dies erfordert genaue Planung der Stillstände, insbesondere in Industriebetrieben, wo Wärme oft prozesskritisch ist. Facility Manager müssen daher Wartungsfenster bestimmen (oft im Sommer oder während Produktionspausen), Ersatzwärmequellen bereitstellen oder den Prozessablauf so anpassen, dass Prüfungen durchgeführt werden können, ohne die Kernproduktion zu gefährden. Operativ ist zudem die Koordination externer Prüfdienstleister bedeutsam: ZÜS-Prüfer, Schornsteinfeger, Servicetechniker – all diese müssen rechtzeitig beauftragt und terminiert werden. Ein verpasster Prüftermin kann nicht nur rechtlich problematisch sein, sondern auch praktische Folgen haben (etwa wenn der Schornsteinfeger die Anlage bei gravierenden Mängeln stilllegt). Daher implementieren viele Betriebe Prüftermin-Überwachungssysteme (z. B. Software, Teil eines CAFM-Systems), die frühzeitig an bevorstehende Prüfungen erinnern. Operativ relevant ist auch die Material- und Ersatzteilvorhaltung: Erkennt eine Inspektion einen Mangel (z. B. defekte Dichtung, Korrosion am Kesselrohr), sollte idealerweise unmittelbar eine Instandsetzung erfolgen. Das setzt voraus, dass Ersatzteile oder zumindest Provisorien verfügbar sind. In der Praxis werden daher oft im Rahmen von Wartungsverträgen Kits bereitgehalten, um Prüfungsfeststellungen sofort abstellen zu können (z. B. Austausch eines Sicherheitsventils bei Versagen in der Prüfung).
Personal und Qualifikation: Operativ stellt sich die Frage, wer die Prüfungen durchführt. Größere Industrieunternehmen haben häufig eigenes Betriebspersonal mit Zusatzqualifikationen, z. B. einen Kesselwärter oder Instandhaltungsingenieur, der als „zur Prüfung befähigte Person“ nach BetrSichV fungieren kann. Dieser kann dann bestimmte wiederkehrende Prüfungen selbst abnehmen, was Flexibilität schafft. In anderen Fällen werden Dienstleister oder Behördenvertreter involviert, was die interne Kommunikation und Abstimmung erfordert. Das Betriebspersonal muss auch für die Prüfungen mitwirken – z. B. Anlage vorbereiten, Druck ablassen, Öffnungen schaffen, Messgeräte anschließen, etc. Dies bedeutet Schulungsaufwand: Mitarbeiter müssen die Prüfvorschriften und Sicherheitsmaßnahmen kennen (etwa beim Umgang mit Druck oder Gas während Prüfungen). Auch das Thema Arbeitssicherheit spielt hinein: Eine Prüfung am druckführenden System darf nur erfolgen, wenn entsprechende Lockout-Tagout-Verfahren angewendet werden, der Prüfraum abgesperrt ist und Schutzausrüstung getragen wird. Facility Manager müssen hier die SOPs (Standardarbeitsanweisungen) definieren, die bei solchen Prüfungen gelten.
Dokumentation und Betriebsführung: Operativ ziehen Prüfungen einen erheblichen Dokumentationsaufwand nach sich. Jedes Prüfergebnis – ob bestanden oder mit Auflagen – muss erfasst, ausgewertet und archiviert werden. Mängelberichte externer Prüfer bedürfen einer Nachverfolgung: Es müssen Fristen gesetzt werden, bis wann z. B. ein beanstandeter Zustand behoben sein muss, und anschließend ist oft eine Wiedervorführung nötig. Dies verlangt ein straffes internes Follow-up-Management. Aus Sicht der ISO 9001 bzw. integrierter Managementsysteme gehören diese Prozesse zum Qualitätsregelkreis (Feststellung – Maßnahme – Wirksamkeitskontrolle). Viele FM-Abteilungen erstellen zu diesem Zweck Prüfprotokolle und Maßnahmenkataloge, die regelmäßig in Team-Besprechungen durchgegangen werden, um sicherzustellen, dass nichts untergeht.
Zusammengefasst wirkt sich das Prüfregime auf den operativen Betrieb insofern aus, als es eine starke Strukturierung und Disziplin erfordert. Ein gut organisiertes Unternehmen zeichnet sich dadurch aus, dass Prüftermine fristgerecht und reibungslos ablaufen, ohne die Produktion zu stören, und dass Befunde umgehend in korrigierende Aktionen übersetzt werden. Dies erfordert ein gewisses Umdenken: Prüfungen dürfen nicht als notwendiges Übel betrachtet werden, sondern als integraler Bestandteil des Betriebs, der aktiv gemanagt werden muss.
Rechtliche und haftungsrelevante Aspekte
Compliance und Aufsichtsbehörden: Die Einhaltung der prüfungsbezogenen Vorschriften ist ein zentraler Teil der Compliance im Facility Management. Viele der genannten Regelwerke (BetrSichV, BImSchV, GEG) unterliegen behördlicher Überwachung durch Ämter wie die Gewerbeaufsicht, das Umweltamt oder Bezirksschornsteinfegermeister. Unternehmen sind verpflichtet, auf Verlangen Nachweise über durchgeführte Prüfungen vorzulegen. So kann die Gewerbeaufsicht etwa im Rahmen einer Betriebsbesichtigung Prüfzertifikate für Druckbehälter verlangen; der Schornsteinfeger händigt sogenannte Feuerstättenbescheide aus, in denen alle Fristen für Emissionsmessungen und Kehrungen festgelegt sind, und kontrolliert deren Einhaltung. Verstöße – etwa ein verpasster Prüfturnus oder das Betreiben einer Anlage trotz durchgefallener Prüfung – können als Ordnungswidrigkeiten mit Bußgeldern sanktioniert werden. In gravierenden Fällen (etwa vorsätzliche Umgehung von Sicherheitsprüfungen) sind sogar Straftatbestände denkbar. Rechtlich brisant ist ferner, dass einige Prüfungen Voraussetzung für die Betriebserlaubnis einer Anlage sind: Beispielsweise darf ein neuer Hochdruckkessel erst in Betrieb gehen, wenn die Abnahmeprüfung durch den Sachverständigen bestanden wurde. Ähnlich muss eine Aufzugsanlage (analoger überwachungsbedürftiger Anlagentyp) alle zwei Jahre eine Hauptprüfung durchlaufen, sonst erlischt der legal konforme Betrieb. Übertragen auf Heiztechnik heißt das: Sollte z. B. ein Dampfkessel die fällige innere Prüfung verpassen, bewegt man sich ab diesem Zeitpunkt in einer Grauzone, die die Versicherungsdeckung gefährden kann und im Schadensfall zu Regreß führt.
Haftung und Betreiberverantwortung: In Deutschland ist die Betreiberverantwortung für technische Anlagen klar umrissen: Der Betreiber (Arbeitgeber, Unternehmen) ist für den sicheren Zustand der Anlage verantwortlich. Kommt es zu einem Unfall (z. B. Kesselexplosion, Kohlenmonoxid-Vergiftung, Brand durch Gasleck) und es stellt sich heraus, dass vorgeschriebene Prüfungen versäumt oder Mängel ignoriert wurden, drohen zivilrechtliche Schadensersatzansprüche und strafrechtliche Folgen (etwa wegen fahrlässiger Körperverletzung oder Tötung). Versicherungen prüfen im Schadenfall genau, ob der Betreiber seinen Prüfpflichten nachgekommen ist; bei grober Vernachlässigung können Leistungen verweigert werden. Umgekehrt kann der Betreiber durch lückenlose Erfüllung aller Prüfvorgaben seine Haftung begrenzen. Sollten dennoch unvorhergesehene Ereignisse eintreten, kann er nachweisen, alle zumutbaren Maßnahmen ergriffen zu haben (Stichwort: Exkulpation durch organisatorische Vorkehr). Daher ist in vielen Unternehmen die Betreiberverantwortung formal delegiert – beispielsweise an den Leiter Facility Management – und dieser sorgt im eigenen Interesse für ein Compliance-gerechtes Prüfmanagement. Ein weiterer rechtlicher Aspekt ist die Vertragshaftung gegenüber Dritten: In Objekten, die etwa an Mieter verpachtet sind (z. B. Industriefirmen in angemieteten Gebäuden), muss vertraglich klargelegt sein, wer die Prüfpflichten trägt. Üblicherweise verbleibt die Verantwortung für zentrale Heizungsanlagen beim Eigentümer bzw. dessen FM-Dienstleister. Dennoch muss der Betreiber vor Ort gewährleisten, dass Prüfer Zugang haben und die Anlage zugänglich ist. Missverständnisse hier können zu Haftungsteilungen führen – was alle Beteiligten durch klare Regelungen vermeiden sollten.
Gesetzesänderungen und Pflichtenanpassung: Ein praktisches rechtliches Thema ist auch die Dynamik der Vorschriften. Gesetze wie das GEG oder Verordnungen wie die BImSchV werden im Laufe der Zeit novelliert, was neue Pflichten schaffen kann. Jüngstes Beispiel war die oben erwähnte befristete Heizungscheck-Pflicht 2022/2023. Facility Manager müssen also am Puls der regulatorischen Entwicklung bleiben, um neue Prüfpflichten zu antizipieren. Unterstützung bieten hier Verbände (GEFMA, FM-Anwenderkreise) und Fachpublikationen, die über Änderungen informieren. In großen Firmen ist es üblich, eine Rechtskataster-Liste zu führen, wo alle relevanten Gesetze und technischen Regeln aufgeführt sind, inkl. Angaben, ob alle Forderungen erfüllt werden. Solche Compliance-Übersichten können auch Bestandteil von Audits sein (z. B. ISO 45001 Audit für Arbeitsschutz prüft, ob BetrSichV-Anforderungen umgesetzt sind). Rechtlich gesehen geht es darum, lückenlose Transparenz über Pflichten und deren Erfüllung herzustellen.
Insgesamt sind die rechtlichen Implikationen von Prüfungen im Heiztechnik-Betrieb erheblich. Sie zwingen Organisationen zu klarem Handeln, das heißt zur Implementierung eines Compliance-orientierten Instandhaltungsmanagements. Dies ist nicht nur defensive Pflichterfüllung, sondern – wie im nächsten Abschnitt beleuchtet – auch positiv in die strategische Unternehmensführung einzubetten.
Strategische Bedeutung im industriellen Facility Management
Über die unmittelbaren Betriebspflichten hinaus beeinflusst das Prüfungswesen auch die strategische Ebene des Facility Managements in industriellen Unternehmen:
Risikomanagement und Business Continuity: Strategisch gesehen sind regelmäßige Inspektionen ein Fundament des Risikomanagements. Indem sie Risiken identifizieren (z. B. materialermüdungsbedingte Ausfallrisiken oder Sicherheitslücken), ermöglichen sie es dem Management, proaktiv Gegenmaßnahmen einzuplanen. Viele industrielle Unternehmen integrieren deshalb die Ergebnisse von Prüfungen in ihre Risikobewertungen. Ein Beispiel: Stellt sich bei einer wiederkehrenden Prüfung heraus, dass ein Heizkessel nur noch begrenzte Restlebensdauer hat (etwa durch Rissanzeigen beim Drucktest), so wird dies im Risiko-Register als bedeutendes Risiko (Heizungsausfall, Produktionsstillstand) vermerkt. Daraufhin kann man vorsorglich Ausweichstrategien erarbeiten (z. B. mobile Kesselanlage bereithalten) – ein Konzept der Business Continuity Planung. Prüfungen liefern somit die Datenbasis für fundiertes Risikomanagement. In fortschrittlichen Fällen wird ein risikobasiertes Prüfkonzept selbst zur Strategie: Mittels Methoden wie Risk Based Inspection (RBI) werden Inspektionspläne so optimiert, dass besonders kritische Komponenten häufiger und intensiver geprüft werden, während unkritische Teile mit größeren Intervallen auskommen. Ziel ist es, Sicherheit und Zuverlässigkeit zu maximieren, ohne unnötig Ressourcen zu binden. Eine solche risikoorientierte Instandhaltungsstrategie – wie von TÜV SÜD unter dem Begriff TÜV-RoiM propagiert – ist ein Beispiel, wie Prüfungen zum integralen Bestandteil der Strategie zur Aufrechterhaltung der Betriebsbereitschaft werden. Der Gewinn ist zweifach: Zum einen werden Kosten minimiert, indem Prüfintervalle an den tatsächlichen Bedarf angepasst werden, zum anderen werden unerwartete Ausfälle vermieden, was Wettbewerbsvorteile durch höhere Anlagenverfügbarkeit mit sich bringt.
Nachhaltigkeit und Energieziele: Strategisch haben Unternehmen heutzutage nahezu immer auch Nachhaltigkeitsziele (reduzierter CO₂-Ausstoß, Energieeffizienzsteigerung um X % etc.). Prüfungen an Heizungsanlagen spielen in diesem Zusammenhang eine entscheidende Rolle. Die Heiztechnik ist oft ein Haupteinflussfaktor auf den CO₂-Fußabdruck von Liegenschaften. Indem Effizienzinspektionen wie der DIN 15378-Heizungscheck durchgeführt werden, lassen sich Maßnahmen ableiten, um den Energieverbrauch zu senken – etwa Nachrüsten von Regelungstechnik, Optimieren der Vorlauftemperaturen oder Erneuern alter Pumpen. Diese Inspektions-basierten Optimierungen zahlen direkt auf die Nachhaltigkeitsstrategie ein. Mehr noch: Einige Unternehmen setzen auf kontinuierliches Energiemonitoring ihrer Heizanlagen (via BMS-Building Management System mit Sensorik), was im Prinzip eine dauernde Prüfung der Performance darstellt. Auffälligkeiten (z. B. steigender Gasverbrauch bei gleicher Außentemperatur) werden detektiert und können zu sofortigen Korrekturmaßnahmen führen. Strategisch positioniert man sich damit als energieeffizienter Betrieb, was in Branchen mit hohem Energieeinsatz (Chemie, Lebensmittel, Automotive) inzwischen auch von Investoren und Aufsichtsorganen gefordert wird (Stichwort ESG-Kriterien). VDI 3810 Blatt 3 empfiehlt explizit, ein Energiemanagement für Heizungsanlagen aufzubauen, inklusive Mess- und Monitoringkonzept. Dies unterstreicht, dass Inspektionen und Monitoring eng verzahnt sein sollten. Ein Beispiel: Die regelmäßige Analyse der Kesselwirkungsgrade und Pumpenstromaufnahme kann Teil der KPI (Key Performance Indicators) im Energiemanagement sein, welche im Management-Review betrachtet werden, um strategische Entscheidungen (z. B. Investition in effizientere Kessel) vorzubereiten.
Lebenszyklusoptimierung und Investitionsplanung: Strategisch bedeutsam ist auch der Langfristhorizont. Jede technische Anlage hat einen Lebenszyklus – von Planung, Bau, Betrieb über Alterung bis zur Erneuerung. Prüfungen liefern über die Jahre eine Datenhistorie, die Aufschluss über die Alterungsprozesse der Anlage gibt. Beispielsweise können ansteigende Reparaturbedarfe, häufigere kleine Mängel bei Inspektionen oder sinkende Effizienzkennzahlen Signale sein, dass das Ende der wirtschaftlichen Nutzungsdauer naht. Ein vorausschauendes Facility Management nutzt diese Informationen für die Investitionsplanung: Anstatt von einem plötzlichen, unplanmäßigen Totalausfall überrascht zu werden, wird rechtzeitig der Austausch oder eine grundlegende Sanierung vorgesehen. Das minimiert Life-Cycle-Costs, weil man höhere Instandhaltungskosten im Alter vermeidet und auch Folgeschäden durch Ausfälle verhindert. In vielen Fällen wird z. B. nach 20 Betriebsjahren ein Kessel so genau überwacht, dass man seinen Austausch auf vielleicht 25 Jahre festlegen kann, bevor die Ausfallwahrscheinlichkeit exponentiell steigt. Diese Entscheidungsfindung wird durch die Inspektionsberichte und Trendanalysen untermauert. Strategisch kann man also sagen: Inspektionsroutinen sichern den Wert der Anlage und ermöglichen planbare Erneuerungsinvestitionen. Das Konzept des Lebenszyklusmanagements in der Immobilienwirtschaft betont, dass frühzeitige Investitionen in Wartung/Inspektion langfristig Gesamtkosten sparen – ein Gedanke, der auf Top-Management-Ebene verstanden und getragen werden muss.
Reputation und Stakeholdervertrauen: Last but not least hat ein vorbildliches Prüf- und Instandhaltungsmanagement auch weiche strategische Effekte. Unternehmen, die nachweislich hohe Sicherheitsstandards einhalten und umweltbewusst mit ihrer Technik umgehen, stärken ihr Ansehen bei Mitarbeitern, Behörden und Öffentlichkeit. Gerade in sensiblen Branchen (etwa Lebensmittel mit Dampfkesseln oder Pharma) wird von Kunden oft erwartet, dass die Versorgungsinfrastruktur robust abgesichert ist. Auditierungen durch Geschäftspartner beinhalten gelegentlich auch die Frage nach Wartungs- und Prüfkonzepten der technischen Anlagen. Ein lückenloses System signalisiert Professionalität und Zuverlässigkeit. Intern fördert es zudem die Sicherheitskultur: Mitarbeiter erleben, dass Sicherheit und Qualität im Betrieb oberste Priorität haben – das kann die Motivation und Achtsamkeit erhöhen.
Es lässt sich festhalten, dass Prüfungen im Heiztechnik-Betrieb nicht isoliert als technische Notwendigkeit gesehen werden dürfen, sondern als strategisches Instrument, um Unternehmensziele in den Bereichen Sicherheit, Zuverlässigkeit, Nachhaltigkeit und Effizienz zu erreichen. Ein discipliniertes Prüfregime ist Kennzeichen eines gut geführten Unternehmens und schafft die Voraussetzungen dafür, auf Dauer erfolgreich und verantwortungsvoll zu wirtschaften.
Einfluss von Inspektionsroutinen auf Risikomanagement, Compliance und Lebenszyklus
In den vorhergehenden Abschnitten wurden bereits viele Querverbindungen zwischen Prüfungen und den Themen Risikomanagement, Compliance sowie Lebenszyklusoptimierung aufgezeigt. Dieser Teil fasst die Kernaussagen noch einmal gezielt unter diesen drei Perspektiven zusammen und vertieft sie.
Risikomanagement durch Prüfungen
Regelmäßige Inspektionen in der Heiztechnik fungieren als Sensoren des Risikomanagements. Jedes Prüfergebnis reduziert die Unsicherheit über den Zustand der Anlage – das ist genau, was Risikomanagement benötigt: verlässliche Informationen. Durch Prüfungen werden Gefährdungen identifiziert und quantifiziert. Beispielsweise kann eine Druckbehälterprüfung Haarrisse im Material offenbaren, was auf ein Schadensrisiko hinweist; oder die CO-Messung zeigt leicht erhöhte Werte, ein Indiz für eine Verbrennungsstörung mit Potenzial für gefährliche Kohlenmonoxidbildung. Solche Erkenntnisse fließen unmittelbar in den Risikobewertungsprozess ein. In methodischer Hinsicht lässt sich dies an FMEA (Failure Mode and Effects Analysis) oder HAZOP-Analysen veranschaulichen: In vielen Fällen werden periodisch die möglichen Ausfallarten der Heiztechnik bewertet – und Inspektionsroutinen stellen sicher, dass die Auftretenswahrscheinlichkeit niedrig bleibt bzw. früh gegengesteuert wird.
Ein konsequentes Prüfregime ermöglicht auch Statistiken über Beinahe-Störungen. So kann man etwa über 10 Jahre auswerten, wie oft ein Sicherheitsventil bei der Prüfung nicht auf Anhieb öffnete oder wie häufig die Schornsteinfeger-Messung gerade noch innerhalb des Grenzwerts lag. Diese Daten erlauben es, Trends abzulesen – steigen die Befundraten, muss das Risiko im Gesamtkontext höher eingestuft werden. Ohne Inspektionen wäre man quasi blind und würde evtl. erst vom tatsächlichen Ausfall „überrascht“.
In der Industrie hat sich daher das Paradigma der vorausschauenden Instandhaltung (Predictive Maintenance) etabliert, das eng mit Prüfungen verwoben ist. Mit IoT-Sensoren und Datenanalytik lassen sich kontinuierlich Zustandsgrößen erfassen und auswerten. Das ist eine kontinuierliche Form der Inspektion. Algorithmen können auf Basis dieser Daten vorhersagen, wann ein Bauteil wahrscheinlich ausfällt – also das Risiko in die Zukunft projizieren. Solche Verfahren, unterstützt durch KI und Big Data, gewinnen aktuell stark an Bedeutung. In Bezug auf Heizungsanlagen kann das bedeuten: Sensoren messen permanent Kesseltemperaturen, Drücke, Abgaswerte; eine Analytics-Software erkennt Muster, die auf Verschlechterung hindeuten, und gibt rechtzeitig Alarm. Damit wird Risikomanagement in Echtzeit betrieben.
Darüber hinaus tragen Inspektionsroutinen auch zu einer Krisenprävention bei. Indem sie Risiken begrenzen, reduzieren sie die Wahrscheinlichkeit von Notfällen (etwa ein Heizungsausfall im Winter, der Produktion und Gebäude gefährdet). Viele Unternehmen haben Notfallpläne, in denen definiert ist, was im Worst Case zu tun ist. Doch ebenso wichtig ist der prophylaktische Teil: Die beste Krisenbewältigung ist eine verhinderte Krise. Prüfungen sind hier die erste Verteidigungslinie. Insofern sind sie ein unverzichtbarer Teil der Resilienzstrategie: Ein Betrieb, der seine Heiztechnik regelmäßig überprüft und wartet, wird von äußeren Stressoren (Kältewellen, Energieversorgungsschwankungen) weniger in die Knie gezwungen als ein unvorbereiteter.
Prüfungen verwandeln unbekannte Risiken in bekannte, beherrschbare Größen. Sie sind ein essenzieller Bestandteil des Risikomanagement-Regelkreises, indem sie Eingangsgrößen für die Risikoanalyse liefern und zugleich wirksame Maßnahmen zur Risikoreduktion darstellen.
Prüfungen als Grundlage der Compliance-Sicherung
Compliance – die Einhaltung aller relevanten Vorschriften – ist, wie dargelegt, im technischen Betrieb unabdingbar. Inspektionsroutinen sind quasi die Checkpoints der Compliance. Sie garantieren, dass gesetzliche Forderungen im Tagesgeschäft umgesetzt werden. Ohne planmäßige Prüfungen würde die Einhaltung vieler Bestimmungen dem Zufall überlassen, was für professionelle Unternehmen indiskutabel ist.
Wichtig ist hier das Prinzip der lückenlosen Nachweisführung. Jede durchgeführte Prüfung generiert ein Protokoll, ein Messbericht, ein Zertifikat. Diese Dokumente sind der Compliance-Nachweis gegenüber Dritten. In Audits (sei es interne Audits, Kunden-Audits oder behördliche Überprüfungen) wird gezielt nach diesen Nachweisen gefragt: „Zeigen Sie mir das Prüfbuch Ihrer Druckbehälter“ oder „Liegen die Emissionsmessberichte der letzten 3 Jahre vor?“. Ein geordnetes Prüfmanagement führt daher akribisch Buch. Viele Betriebe digitalisieren diesen Prozess inzwischen: In Instandhaltungs- und Compliance-Software werden die Prüftermine, Ergebnisse und Dokumente hinterlegt, sodass im Bedarfsfall auf Knopfdruck Reports erzeugt werden können. Das erleichtert es beispielsweise, für ein anstehendes Zertifizierungsaudit (z. B. ISO 14001 Umweltmanagement) dem Auditor eine komplette Liste aller prüfpflichtigen Anlagen und deren Status vorzulegen – was die Glaubwürdigkeit des Compliance-Systems untermauert.
Zudem dient die Umsetzung der Prüfpflichten auch der Haftungsabwehr und Rechtscompliance in einem weiteren Sinne: Sie zeigt, dass das Unternehmen seiner organisatorischen Sorgfaltspflicht nachkommt. Im deutschen Recht gibt es den Begriff der „Organisationsverschuldung“: Ein Unternehmensleiter kann haftbar sein, wenn er kein angemessenes Organisationskonzept hatte, das Rechtsverletzungen verhindert. Ein gut organisiertes Prüfregime ist quasi ein Beleg gelebter Legalität – es reduziert das Risiko, wegen Fahrlässigkeit belangt zu werden. Sollte es dennoch zu Zwischenfällen kommen, kann sich das Unternehmen zumindest entlasten, da es nachweislich alle vorgeschriebenen Maßnahmen ergriffen hatte.
In Branchen mit strenger Regulierung (z. B. Kraftwerke, Chemieanlagen) gehören Inspektions-Compliance-Daten oft zu Kennzahlen. Es wird intern gemessen, wie hoch die Quote fristgerecht geprüfter Anlagen ist (idealerweise 100 %) und Abweichungen werden sofort gemeldet. Dieses Monitoring der Compliance im Bereich Prüfungen hat in den letzten Jahren zugenommen, da Stakeholder (Aufsichtsräte, Versicherer) verstärkt darauf achten. Schließlich können Versäumnisse sehr teuer werden, wenn z. B. eine nicht geprüfte Anlage einen Schaden verursacht, den die Versicherung dann nicht deckt.
Insofern bilden die Inspektionsroutinen eine tragende Säule der Compliance-Kultur im Facility Management. Sie verknüpfen technische Pflichterfüllung mit rechtlicher Absicherung. Das Bewusstsein dafür muss bis in die Führungsriege reichen, damit die nötigen Ressourcen und Rückendeckung bereitgestellt werden. Im Idealfall wird Compliance nicht als Belastung, sondern als Qualitätsmerkmal verstanden – ein Unternehmen, das streng auf Prüfung und Sicherheit achtet, demonstriert Integrität in seinem Handeln.
Lebenszyklusoptimierung und Anlagenwertsteigerung
Wie bereits angeklungen, beeinflussen regelmäßige Prüfungen maßgeblich den Lebenszyklus einer Heizungsanlage. Dies lässt sich in mehreren Phasen betrachten:
Inbetriebnahme und Hochlauf: Schon beim Start einer neuen Anlage setzen Prüfungen den Grundstein für ein langes Leben. Die Abnahmeprüfungen (Druckprobe, Funktionsprüfungen) stellen sicher, dass mit einer fehlerfreien Basis begonnen wird. In der Einfahrphase folgen oft engmaschige Inspektionen (z. B. Inspektion nach 1000 Betriebsstunden), um „Kinderkrankheiten“ zu beheben. Diese frühe Phase entscheidet oft über die Lebensdauer – wenn hier Mängel übersehen werden, können sie später größeren Schaden anrichten. Ein Beispiel: Wird bei der Abnahme versäumt, einen leicht klemmenden Brennstoffabsperrschieber zu beanstanden, könnte dies Jahre später zu einem ernsten Sicherheitsproblem führen. Daher gilt: Sorgfältige Prüfungen zu Beginn zahlen sich in verlängerter Lebensdauer aus.
Nutzungsphase: Während der regulären Nutzungszeit einer Anlage haben Inspektionsroutinen die Funktion einer Gesundheitsvorsorge. Ähnlich wie regelmäßige Arztbesuche beim Menschen bewirken, dass Krankheiten früh erkannt und behandelt werden, sorgen Anlagenprüfungen dafür, dass die „Wehwehchen“ des Kessels oder Systems nicht eskalieren. So verlängern z. B. regelmäßige Reinigungsinspektionen (bei denen z.B. Heizflächen gereinigt werden, eine Art Wartung im Zuge der Inspektion) die Lebensdauer, weil sie Korrosions- und Ablagerungsprozesse verlangsamen. Auch das rechtzeitige Ersetzen von Verschleißteilen (Dichtungen, Lager, Ventilsitze) infolge von Inspektionsbefunden beugt größeren Schäden vor. Studien zu Lebenszykluskosten zeigen, dass eine präventive Instandhaltung zwar laufende Kosten verursacht, aber teure Anlagenausfälle und Frühausfälle deutlich reduziert, was in Summe wirtschaftlicher ist.
Alterungs- und Aussonderungsphase: Gegen Ende der technischen Lebensdauer einer Heizungsanlage (typisch 20–30 Jahre) liefern die Prüfungen entscheidende Hinweise für den optimalen Austauschzeitpunkt. Wenn die Inspektionen zunehmend Mängel zutage fördern, die nur mit hohem Aufwand behoben werden können, oder wenn die Effizienzmessungen zeigen, dass die Anlage selbst bei einwandfreiem Zustand nicht mehr zeitgemäß ist, dann ist der ökonomische Kipppunkt erreicht. Indem solche Informationen aus Prüfungen systematisch erfasst werden, kann die Entscheidung für einen Austausch oder eine Großüberholung datenbasiert und vorausschauend getroffen werden. Beispielsweise könnte ein Betreiber feststellen: „Unser Hauptkessel hat in den letzten drei Jahren jeweils erhebliche Reparaturkosten nach den TÜV-Prüfungen verursacht und kommt nur noch auf 85 % Wirkungsgrad – wir planen in zwei Jahren die Investition in einen neuen Brennwertkessel.“ Diese Planung ist dem reaktiven „Kaputt warten“ weit überlegen, da sie Zeit für Ausschreibung, Finanzierung und Installation lässt, ohne Notdruck einer havarierten Anlage.
Restwert und Wiederverkauf: In manchen Fällen werden noch funktionstüchtige Anlagen verkauft oder umgesetzt (z. B. bei Werksschließung oder Umnutzung). Ein lückenlos gewarteter und geprüfter Heizkessel hat einen höheren Restwert am Gebrauchtmarkt als ein gleichaltriger Kessel unbekannten Zustands. Die Prüfberichte dienen hier wie ein „Scheckheft“ beim Auto als Vertrauensgrundlage. Auch das ist ein Nebeneffekt: Instandhaltungsnachweise erhalten den Anlagenwert.
Optimierung des Anlagendesigns: Eine langfristige Betrachtung mehrerer Lebenszyklen kann auch zu Feedback ins Engineering führen. Wenn ein Unternehmen z. B. feststellt, dass bestimmte Kesseltypen in der Wartung immer wieder ähnliche Probleme zeigen (erkennbar in Inspektionsprotokollen), wird es bei Neubeschaffungen diese Erfahrungen berücksichtigen. So fließen praktische Inspektionserkenntnisse in die Anlagenauswahl und -auslegung zukünftiger Generationen ein. Dies optimiert den gesamten Anlagenbestand über die Jahre.
Es tragen Inspektionsroutinen damit entscheidend zur Wirtschaftlichkeit über den gesamten Lebenszyklus bei. Sie minimieren unproduktive Stillstandszeiten, verteilen Kosten planbarer und verhindern teure Schäden. In der Summe kann man sagen: Ohne Inspektionen altert eine Anlage unkontrolliert und stirbt früh; mit Inspektionen altert sie in Würde und leistet maximalen Ertrag bis zum geplanten Lebensende.
Aktuelle Praxis, Herausforderungen und Innovationen im Prüfungsmanagement
Nachdem die Grundlagen, Abläufe und strategischen Zusammenhänge erläutert wurden, soll zum Abschluss der Blick auf die gegenwärtige Praxis und zukünftige Entwicklungen gerichtet werden. Welche Herausforderungen stellen sich beim Management von Heizungsprüfungen heute, und welche Innovationen zeichnen sich ab, um diese Aufgaben effizienter und effektiver zu gestalten?
Status quo und Herausforderungen in der Praxis
Heterogene Anlagenlandschaft: Eine Herausforderung ist die Vielfalt der Anlagen und Zuständigkeiten. In Industrieunternehmen gibt es oft ein Nebeneinander von Gebäudeheizungen (Gebäudemanagement) und Prozessheizungen (Produktionsinfrastruktur), die unterschiedlichen Regularien folgen können. Prozess-Dampfkessel unterliegen z.B. strengeren Prüfregimes als ein Warmwasserkessel fürs Verwaltungsgebäude. Die Koordination dieser unterschiedlichen Anforderungen erfordert breites Know-how und organisatorische Abstimmung zwischen Abteilungen. Ein häufiger Schwachpunkt ist eine fehlende Gesamtübersicht – Unternehmen lösen das zunehmend, indem sie alle prüfpflichtigen Objekte in zentralen Datenbanken erfassen und dem Facility Manager die Gesamtverantwortung übertragen, auch wenn operative Durchführung dezentral erfolgt.
Dokumentationslücken und Altdaten: In der Praxis existieren nicht selten Lücken in den historischen Aufzeichnungen. Insbesondere bei älteren Anlagen oder nach Betreiberwechsel fehlen mitunter Prüfprotokolle aus früheren Jahren. Das erschwert die Trendbeobachtung und kann bei Behördennachfragen problematisch sein. Für Facility Manager besteht die Herausforderung, solche Lücken möglichst schnell zu schließen: Durch Nachmessungen, Neubewertungen oder das Einholen von Kopien bei Prüforganisationen. Einmal etabliert, sollte ein digitales System künftig verhindern, dass erneut Daten verloren gehen.
Kapazitätsengpässe und Fachkräftemangel: Deutschlandweit wird berichtet, dass Prüforganisationen stark ausgelastet sind – z.B. haben TÜV/DEKRA-Prüfer volle Terminkalender, Schornsteinfeger haben Personalengpässe. Für Betreiber heißt das, Prüfungen müssen sehr langfristig geplant werden, um Fristen zu halten. Kurzfristige Prüfwünsche, etwa nach Änderungen an Anlagen, sind teils schwer zu erfüllen. Auch intern spüren Unternehmen den Fachkräftemangel im technischen Facility Management. Erfahrenes Personal, das die Prüfprozesse kennt, geht in Rente; Nachfolger sind nicht immer sofort mit allen Pflichten vertraut. Das erfordert intensivere Schulung und Wissensmanagement. Einige Unternehmen begegnen dem, indem sie externe Spezialisten für das Prüfmanagement hinzuziehen oder dies an FM-Dienstleister auslagern. Die Herausforderung bleibt aber, die Kompetenz im Haus ausreichend zu haben, um die richtigen Entscheidungen zu treffen und externe richtig steuern zu können.
Kosten- und Effizienzdruck: Prüfungen verursachen Kosten – nicht nur direkt (Prüfgebühren, Messdienstleister) sondern auch indirekt durch mögliche Stillstandszeiten oder Personalaufwand. Im Industrieumfeld steht Facility Management oft unter Spardruck, da es als „Kostenstelle“ gilt. Hier die Balance zu halten zwischen Kosteneffizienz und Einhaltung aller Prüfungen ist ein Drahtseilakt. Kurzfristige Sparmaßnahmen (z. B. Prüfintervalle bis ans erlaubte Maximum dehnen, Wartungen seltener vergeben) können langfristig teuer zu stehen kommen. Dennoch sieht man in der Praxis teils eine „auf Kante genähte“ Planung, wo Puffer fehlen – etwa wird eine Prüfung genau am letztmöglichen Termin gemacht, Ausfälle werden in Kauf genommen. Diese Mentalität zu ändern hin zu einem proaktiveren Ansatz ist kulturell eine Aufgabe. Erschwerend kommt hinzu, dass der Nutzen von Prüfungen oft unsichtbar bleibt („es ist ja nichts passiert, warum so viel Aufwand?“). Hier müssen FM-Manager gutes Argumentieren beherrschen und mit Zahlen belegen, dass Prävention günstiger ist als Reaktion – was zum Glück durch viele Erfahrungswerte belegt werden kann (Verschlechterung des Wirkungsgrads um 1 % kostet mehr als die jährliche Messung, wie es ein Schornsteinfeger werbend ausdrückte).
Sich wandelnde Regularien und Technik: Eine weitere Herausforderung ist die Dynamik in Technik und Vorschriften. Aktuell beispielsweise ist die Transformation der Heiztechnik im Gange – Stichwort Dekarbonisierung (Umstieg auf Wärmepumpen, Biomasse, Wasserstoff). Dies bringt neue Anlagentypen, für die teils andere Prüfkonzepte gelten (z. B. Prüfen von Wärmepumpen auf Dichtheit des Kältemittelkreislaufs nach F-Gase-Verordnung). Facility Manager stehen vor der Aufgabe, ihr Prüf-Portfolio laufend zu aktualisieren, wenn neue Technologien eingeführt werden. Ebenso ändern sich Vorschriften: Die GEG-Novelle 2024, die Neuauflage der 1. BImSchV etc. – es gilt, am Ball zu bleiben. Dies kann ressourcenintensiv sein, da man ständig Fachinformationen auswerten muss. Unterstützung gibt es hier durch Verbände und teils digitale Tools, aber letztlich muss im Unternehmen jemand verantwortlich sein, diese Änderungen zu implementieren.
Es liegt die praktische Herausforderung darin, ein umfangreiches, komplexes Aufgabenpaket zuverlässig und ökonomisch sinnvoll zu bewältigen, gegen widrige Umstände wie Personalknappheit und Kostendruck. Es bedarf klarer Prozesse, guter IT-Unterstützung und eines Bewusstseins aller Beteiligten für die Wichtigkeit der Prüfaufgaben.
Innovative Ansätze und zukünftige Entwicklungen
Die gute Nachricht ist: Es gibt eine Reihe von Innovationen und Trends, die darauf abzielen, das Prüfungsmanagement im Facility Management zu erleichtern und zu verbessern:
Digitalisierung und Smart Maintenance: Wie in vielen Bereichen hält die Digitalisierung auch hier Einzug. Moderne CAFM-Software (Computer Aided Facility Management) beinhaltet Module für Prüfterminsteuerung, automatische Erinnerungen und Workflows, die vom Prüftermin bis zum Mängelmanagement alles abbilden. Das minimiert die Gefahr menschlichen Versagens (z. B. einen Termin zu übersehen). Darüber hinaus ermöglichen mobile Endgeräte (Tablets mit Prüf-Apps) dem Prüfer vor Ort, Befunde sofort zu dokumentieren und zentral zu speichern. Damit werden auch Revisionssicherheit und Zugriff verbessert – jeder berechtigte Nutzer kann alle Prüfberichte z.B. in der Cloud einsehen, was die Transparenz steigert.
Internet of Things (IoT) und kontinuierliche Überwachung: Bereits angesprochen wurde die Ausstattung von Anlagen mit Sensoren, die Zustandsdaten liefern. Diese Entwicklung wird sich fortsetzen. Immer mehr Bestandteile einer Heizungsanlage werden „smart“: Pumpen melden ihre Betriebsstunden und etwaige Störungen, Gaszähler liefern Verbrauchsprofile in Echtzeit, Temperaturfühler überwachen die Verteilung. Integriert in ein Building Management System (BMS) oder eine IoT-Plattform, entstehen so digitale Zwillinge der Anlage. Die Vision ist, dass eines Tages viele bisher manuell durchgeführte Prüfungen automatisiert werden können. Beispielsweise könnte ein selbstüberwachender Kessel seine Emissionen fortlaufend messen und dem Schornsteinfeger eine digitale Konformitätserklärung senden – in Ansätzen gibt es so etwas bereits (Stichwort Fernüberwachung anstelle der 2- oder 3-jährigen Messung, sofern gesetzlich zugelassen). Diese Automatisierung entlastet das Personal und macht Prüfungen effizienter, muss aber natürlich zuverlässig und manipulationssicher sein.
Künstliche Intelligenz und Predictive Analytics: KI kommt ins Spiel, wenn es darum geht, aus der Fülle von Sensordaten sinnvolle Vorhersagen zu treffen. Ein KI-System könnte z. B. anhand von historischen Daten lernen, wann ein Heizkesseltyp erfahrungsgemäß Probleme bekommt, und weit im Voraus warnen „In 6 Monaten wird vermutlich die Brennerleistung nachlassen – plane eine Wartung ein“. Solche Model Predictive Controls und Analysen werden bereits pilotiert und könnten die Prüfintervalle flexibler machen, wie es risikobasierte Ansätze fordern. Statt starrem Kalender könnten Prüfungen dann bedarfsgerecht erfolgen – wenn die Datenanzeichen es nahelegen. Das erhöht die Effektivität und schont Ressourcen dort, wo alles in Ordnung ist.